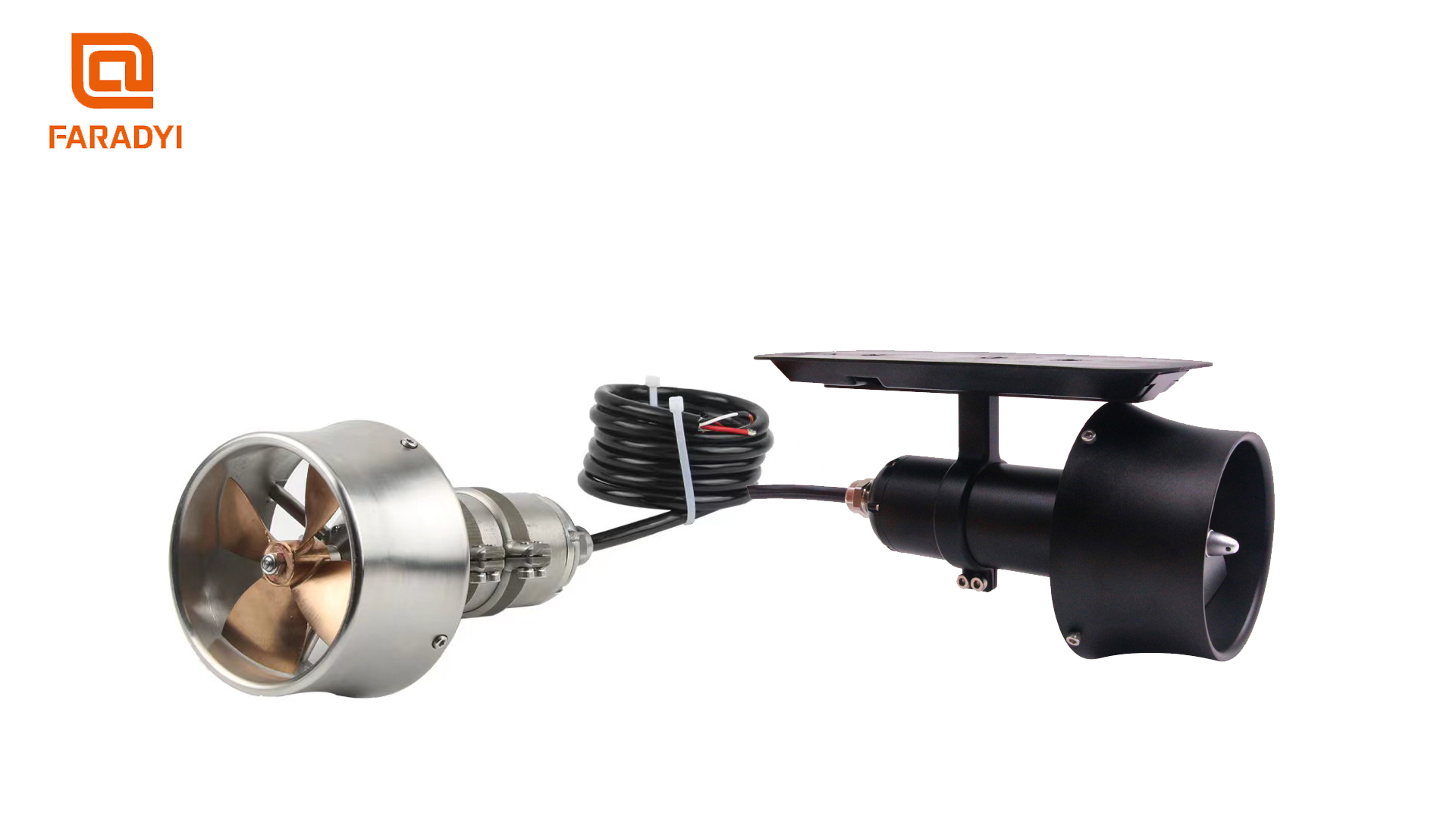
Factors Affecting the Rated Current of Brushless DC Motors
The rated current of brushless DC motors is generally required by users, which involves the power of the DC power supply selected by the user and the amount of discharge (ampere-hour).
The rated current of brushless DC motors is generally required by users, which involves the power of the DC power supply selected by the user and the amount of discharge (ampere-hour).
To use tooth flux as the working flux of brushless DC motor, it is necessary to conduct some quantitative analysis on tooth magnetic induction intensity and find out some quantities related to tooth flux density and their mutual relationship so as to serve as the basis for judgment and design
Brushless motors are composed of permanent magnet rotors, multi-pole winding stators, position sensors, etc. The position sensor changes the rotor position and commutates the current of the stator winding in a certain order (that is, it detects the position of the rotor pole relative to the stator winding, and generates
In the process of using a brushless motor, we may encounter abnormalities such as high temperature or smoke. When such problems occur, we can check the motor from the following points. Let’s discuss them together today.
Causes of brushless DC motor overheating may include motor overload, low load power factor, too low speed, winding short circuit, abnormal voltage, unbalanced power supply, wiring errors, winding failure, bearing damage, excessive load, mechanical failure, frequent starting, High-temperature environments, dust and oil accumulation, and air duct obstructions require corresponding adjustments,
The two-phase hybrid stepper motor is an open-loop control motor that converts electrical pulse signals into angular displacement or linear displacement. It is the main executive element in modern digital program control systems and is widely used.
The three-phase hybrid stepper motor is an induction motor. Its working principle is to use electronic circuits to convert DC power into time-sharing power supply. The multi-phase timing controls the current and uses this current to power the stepper motor. The stepper motor In order to work normally, the driver
The use of stepper motors is limited by working environmental conditions, including factors such as temperature, humidity, and dust. The standard models provided by the manufacturer are suitable for installation under good environmental conditions, but under special circumstances it is necessary to discuss the order with the manufacturer. Pay special
Compared with the sine wave drive, the brushless DC motor square wave drive has the advantages of simplicity, low cost, and high material utilization, but it has the disadvantages of large torque ripple. However, with good design and control, square wave drives can reach the level of brushed DC servo
Brushless DC motors (BLDC) offer simplicity in construction, reliability in operation, and ease of maintenance due to the absence of commutator, brushes, or slip rings, compared to traditional AC and DC motors.
Faradyi manufactures high-quality brushless motors for aviation, robotics, medical, auto, machinery, new energy, and infrastructure industries globally.
Faradyi Motor Has Been Deeply Involved In The Motor Industry For Decades, Specializing In The Production Of Various Robots And Brushless Motors.Update more new news in real time~